Our Key Processes
Polishing
Our polishing area contains many different ways to polish parts. This skill allows for smooth, friction free movements with minimal geometric distortion. This process we call Geo Gleiss.
When you see the label on a box Geo Gleiss you know that you have a geometrically perfect part with a glass like finish. This will give your tools the edge in terms of performance.
We carefully complete our tools with highly trained technicians. All tools can be superfinished through bespoke automatic processes. This ensures that our product have a consistent finish whilst maintaining a competitive price.
Our technicians work in close combination with the metrology department using scanning and 3D techniques to ensure our tools have low variability.
You will, if specified receive our tools, die and punches with ultra-low friction. This equates to surface finish <Ra0,05mm.
The tools are a true mirror finish – the high level of polish does not alter the geometric perfection of the part allowing for burr free parts where the tool runs for longer between cleans.
Surface finish with Geo-Gleiss
Geo-Gleiss – to serve the world of precision SUMCA has the possibility to deliver the very best in Surface finishes. Attaining <20 nanometers a low friction with absolute precision is ensured. The process is carefully controlled by our professionals who have the measurement tools and the experience to detect problems. Sharp edges – guaranteed, prepared edge breaks – guaranteed. The efficiency is in the detail, we are here to discuss finishing for your process.
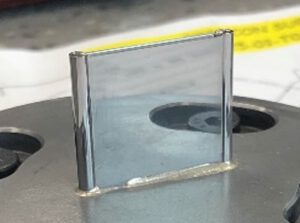
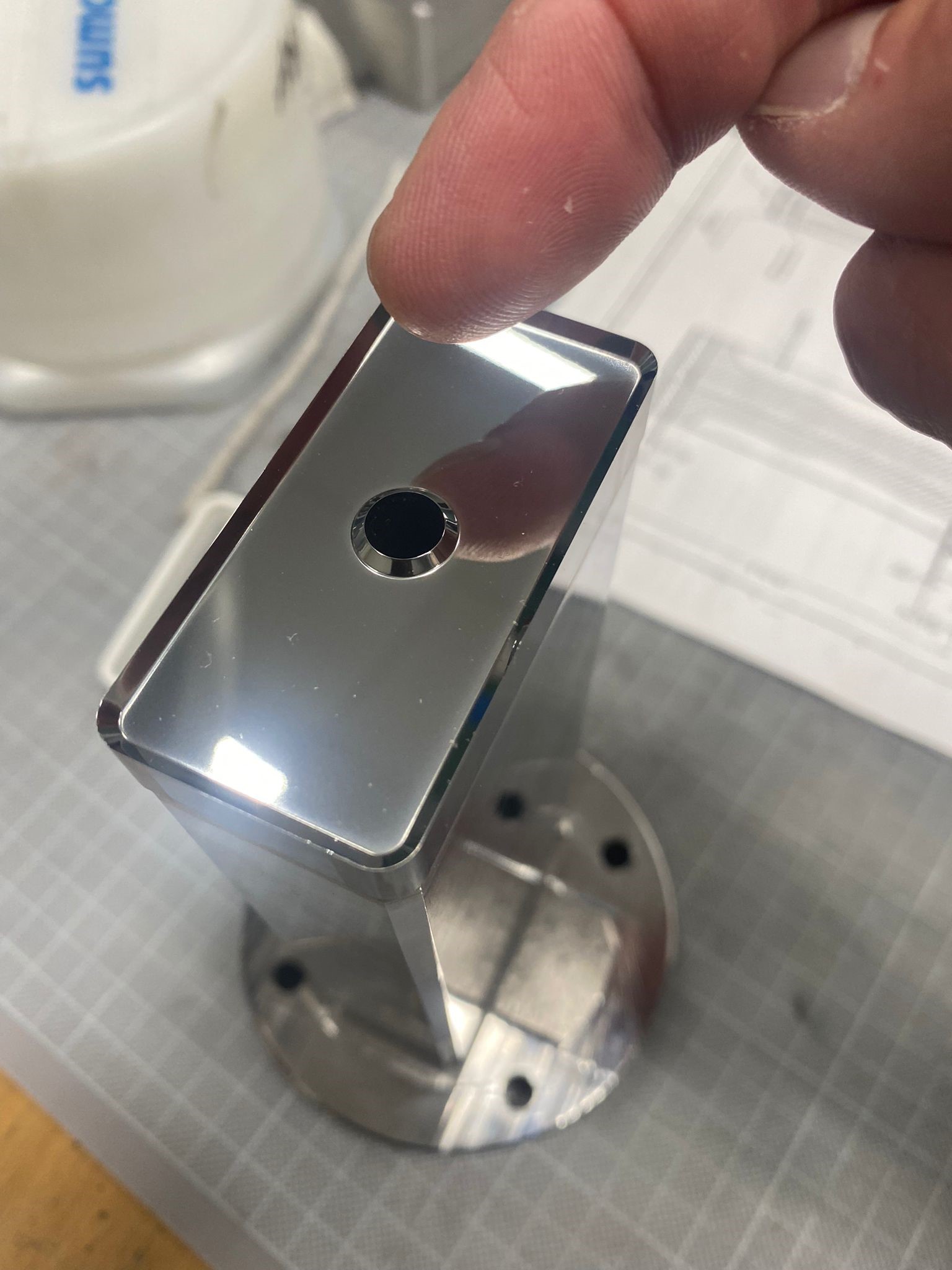
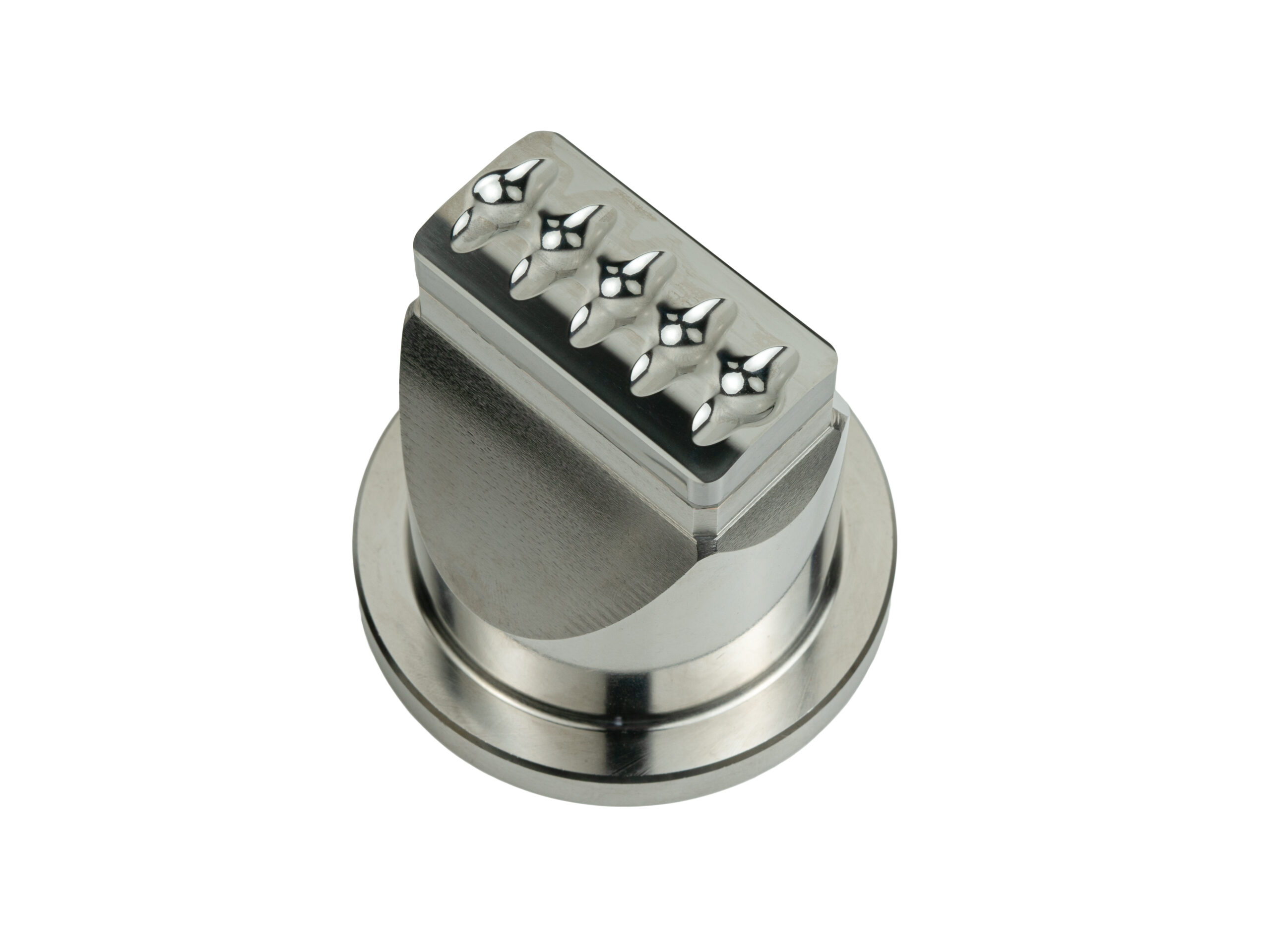
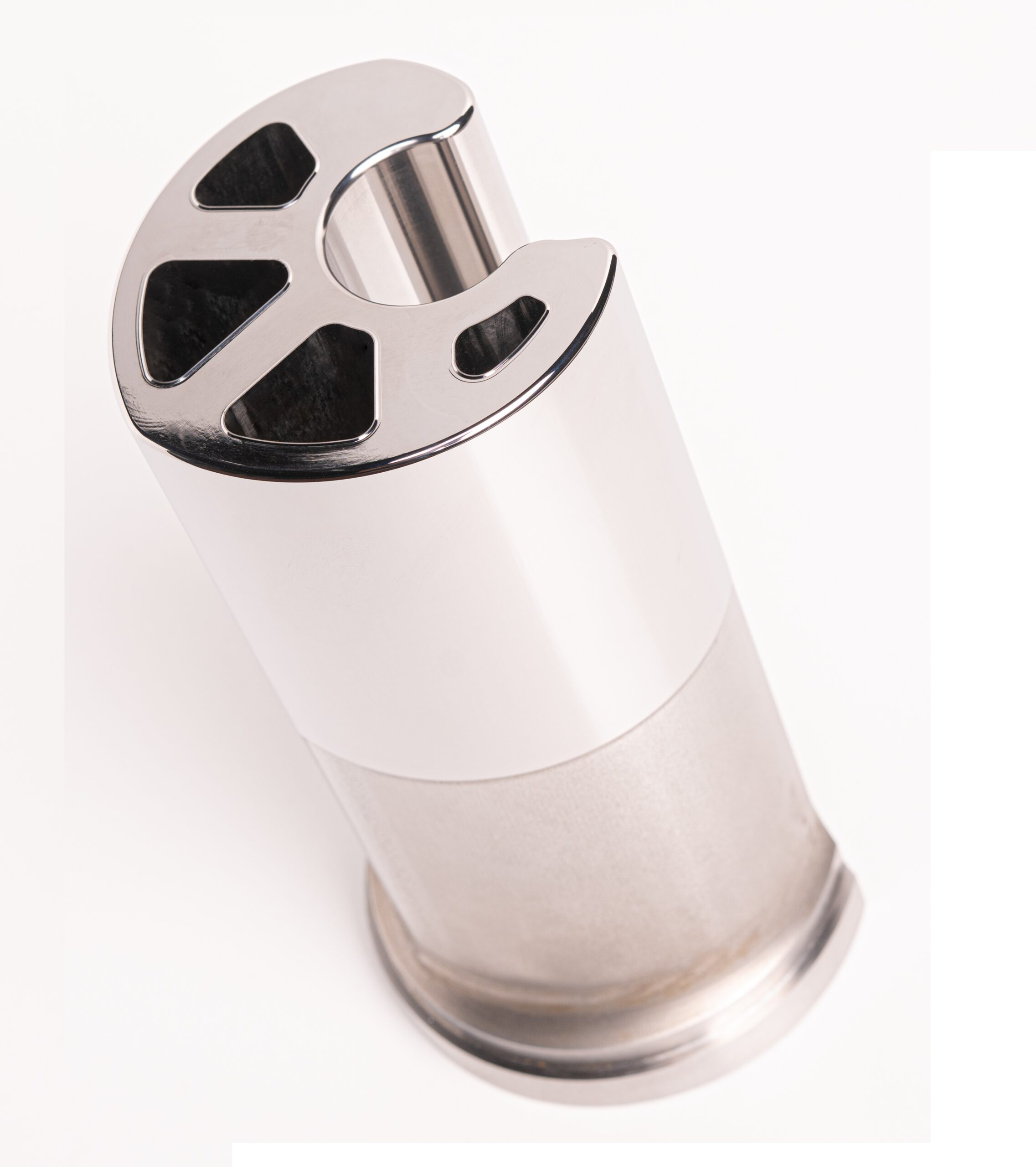
Wire Erosion
Our modern CNC park of wire erosion machines offers our clients the possibility to develop shapes that were not available to the market until the evolution of the 3D model.
We can perfectly match dies that have changes to their shape. Our clients can benefit from a wide range of machines that offer wire diameters:
- 0.12
- 0.2
- 0.25
The knowledge of the group covers carbide (hard metal & hardened steels) all carried out in an air conditioned work shop.
The machines are equipped with Zero Referencing Systems from Erowa, Progrit & System 3R (Macro, Refix & Matrix 142 & 110). These chucks are the same style that are found at our customers.
They ensure that the tools are produced in the same way that they are clamped in the press.
The erosion group is followed by their own CMM and 2D pre-setter allowing our well-trained technicians to be fully autonomous in their day-to-day work.
Sink Erosion
The sink erosion cell is fully robotized, the machines are in production 24/7 allowing for a flexible approach to production scheduling to follow customer requirements closely. The machines are all positioned in modern workshop with LED lighting and fully air-conditioned.
The machines are equipped with Zero Referencing Systems from Erowa, Progrit & System 3R (Macro, Refix & Matrix 142 & 110). These chucks are the same style that are found at our customers. They ensure that the tools are produced in the same way that they are clamped in the press.
The erosion group is followed by their own CMM and 2D pre setter allowing our well-trained technicians to be fully autonomous in their day-to-day work. The technicians have an excellent depth of knowledge in machining carbide (carbide & hardened steels) and work in coordination with the high-speed milling group to ensure the air gap for erosion delivers the perfect form to our clients.
The group stocks a great number of electrodes to support our clients repetitive work and optimize forms, cost and lead times.
Measurement
The quality department was relocated in a custom-built area in 2018. Fully air conditioned to ±1°C with high density LED lighting to ensure that our parts are scrupulously inspected to ensure satisfaction in service.
The company retains five fully trained metrologists capable of running our three CMMs. We have a LEITZ with a full fourth axis and on-board laser scanning, a Mitutoyo STRATOS and two Crystals with continuous contact scanning.
Why the importance of scanning? The ability to compare the theoretical designed part with the manufactured part is of utmost importance. In any die and mould application the air gap 360° is critical to ensure the correct functioning of the tool. The ability to scan forms, however intricate, is essential for the production team to deliver consistent tools.
Our metrologists have no limits with regards to radii measured – whether internal or external the team have the means to guarantee geometry.
With 20 years experience in quick clamping systems the team are adapt at validating the shape of parts relative to a zero reference system. We have two approaches, produce the part directly on the pallet of the quick change system or align the part after production. Both methods are used daily.
Maximum capacity is 400mm height of part for internal forms, 700mm for external with a table size of 1500 x 800 available. For handling typically work pieces are less than 400mm cube.
Grinding
The production of our parts generally will have a grinding phase. Whether this is to prepare the tool for precision finishing in a secondary process or the last operation to finish a critical feature. This allows us to prepare a simple reference surface through to complex evolutive forms.
We offer all varieties of grinding from Surface through to CNC Coordinate Jig Grinding. The tolerances that we can guarantee are sub 2 micron (<0.002mm) geometric error with low distortion mirror finish >0.05Ra.
We are capable of grinding Carbide (Hardmetal), hardened HSS and sintered steel in single piece or batch volumes.
The grinding areas are all temperature controlled for atmosphere and cutting fluids. The technicians are multi-skilled being able to support more than one process.
High Speed Milling (HSM)
Since 2006 Sumca has been exploiting the machining technique of small high speed passes giving fine finish with high precision. The machine park covers 3, 4 and 5 axis high speed machining. Of particular interest is that all machines run in a fully synchronized movement based on the shape required. This ensures that all radii, angles and intersections are correctly interpolated to avoid stress raisers in the tools or the parts pressed. We have machines for the right job with a good lead time.
The process is linked to finishing hardened steels and preparing electrodes for the more demanding applications when an electro-erosion is the only solution.
The machine park is fully optimized with a detailed maintenance regime, the machines are fully robotized operating machines 24/7 allowing for a supple approach in production that allows for flexibility when dealing with customer requirements.
We can produce radii down to R0.05. Our design department or our client will provide the 3D model that we use to produce the electrode or the final tool produced in direct finishing.
The number of technicians that we have available mean that we keep up to date with the latest cutting tool technology through exchanges with tooling, machine and close involvement in third party projects.